Сделать проект автомобиля нетрудно, но трудно его воспроизвести в тысячах экземпляров эффективно, гибко и на высоком качественном уровне. Причем, как бы хорошо мы не сделали машину, она не удовлетворяет нас на будущее».
Вице-президент по производству
компании CHRYSLER Д. Доуч
Как мы отмечали в предыдущих статьях, процесс создания автомобиля весьма условно можно разделить на отдельные стадии, так как работа, как правило, ведется одновременно и при тесном взаимодействии дизайнеров, конструкторов, производственников. Что касается сферы конструирования и производства, то в шутку говорят, что различие между ними зависит от местоимения: «Можем ли МЫ это сделать?» или «Могут ли ОНИ это сделать?». И в том, и в другом случае местоимение обозначает производство — последнее звено в эстафете на пути к готовому автомобилю.
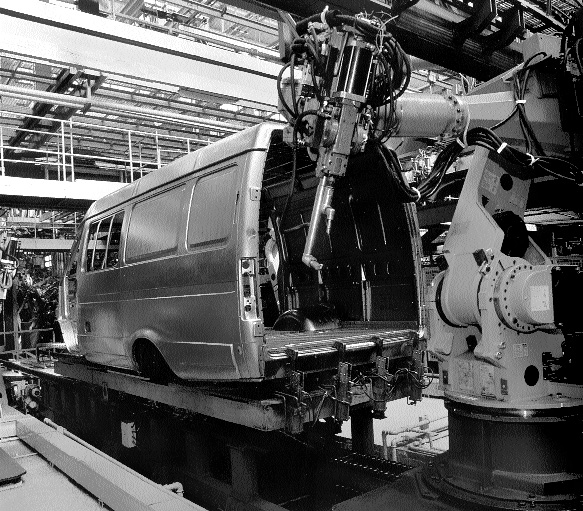
Наиболее интенсивный период подготовки производства начинается примерно за год до планируемого начала выпуска. Еще на стадии отработки макетного образца производственники используют его, чтобы представить себе конкретные моменты технологического процесса. Если при этом возникают проблемы, то в данный момент еще не поздно внести изменения в штампы и другие инструменты, находящиеся на стадии конструирования.
Когда в процессе постройки опытных образцов параметры автомобиля уточнены еще и еще раз, наступает стадия «головного образца», который строится точно в запланированной последовательности сборки — при этом определяются нормы времени, проверяются все ее операции. Такую же проверку проходит производственное оборудование, установленное на линии сборки. В ряде случаев, особенно при разработке принципиально нового автомобиля, некоторые компании изготавливают опытные производственные линии, на которых в лабораторных условиях воспроизводится технологический процесс.
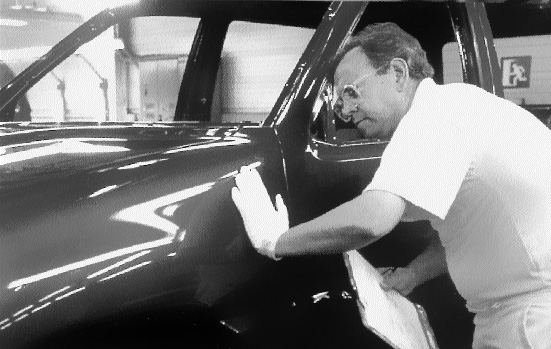
Очередные образцы, в которых учтены все недоработки, уже на 100% должны соответствовать серийным и комплектоваться изделиями, полученными от смежников. Именно эти автомобили подвергаются основному циклу лабораторных испытаний и проходят все предусмотренные дорожные испытания.
Примерно за шесть недель до планируемого начала производства (в компании CHRYSLER) начинается выпуск установочной партии. Автомобиль уже полностью соответствует серийному, вплоть до таких деталей, как фактура обивки сидений, и совсем скоро, пройдя длинный путь от идеи, родившейся в голове дизайнера до конвейера автосборочного завода, он начнет тиражироваться тысячами экземпляров.
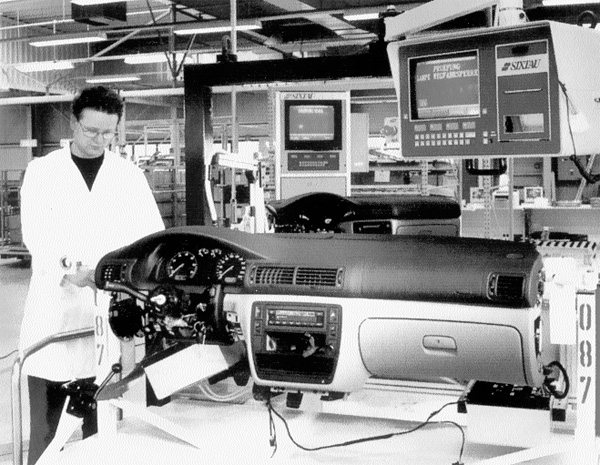
Современный подход к организации производства предусматривает отказ от производства комплектующих и сборки конечного продукта под «одной крышей» в пользу получения готовых узлов и агрегатов от смежников. Таким образом, современный автомобильный завод все чаще представляет собой сборочный, где собственно изготовление ограничивается штамповкой кузовных панелей, производством некоторых пластмассовых изделий и т. п. Разумеется, что при такой организации производства, при огромном количестве сторонних поставщиков, особое внимание должно уделяться построению системы материально-технического снабжения.
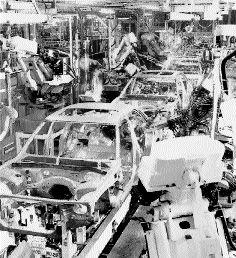
В последние годы во всем мире проявляется пристальный интерес к японской системе «канбан» или «точно-во-время», представляющей собой качественно новую ступень рационализации производства. Смысл работы по этой системе состоит в том, что на всех фазах производственного цикла требуемый узел или деталь поставляются именно тогда, когда это нужно, без создания промежуточных заделов и сведения к минимуму объема товарно-материальных запасов. И такой же подход применяется к снабжению покупными компонентами и комплектующими изделиями. Так, количество складских запасов у фирмы TOYOTA, в какой бы части света не находился завод, рассчитано на один час работы. По различным оценкам, система «канбан» позволяет этой фирме экономить до 94 долларов на себестоимости одного автомобиля.
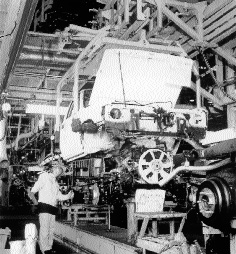
Вполне объяснимо, что такой метод организации производства возник именно в Японии, учитывая естественную нехватку и высокую стоимость земли. Однако стремление сэкономить на складских площадях «потянуло» за собой необходимость пересмотреть всю организацию производства. Прежде всего стал необходим высокий уровень автоматизации, синхронизация производственных процессов во всех фазах и высокая культура производства. При такой системе резко возрастают требования к качеству продукции поставщиков, на которых целиком возлагают ответственность за обеспечение надлежащего уровня качества. Так, в Японии надежному поставщику предоставляют право поставлять детали, минуя входной контроль, непосредственно на линию, где они используются. Для заказчика — очередная экономия на контрольных операциях, а поставщик вынужден переходить на систему бездефектного выпуска продукции. Необходимость выполнения условий системы «канбан» заставляет последних даже строить новые производственные мощности поблизости от основного заказчика. Но, как показывает опыт, расстояния не становятся препятствием для внедрения этого прогрессивного метода.
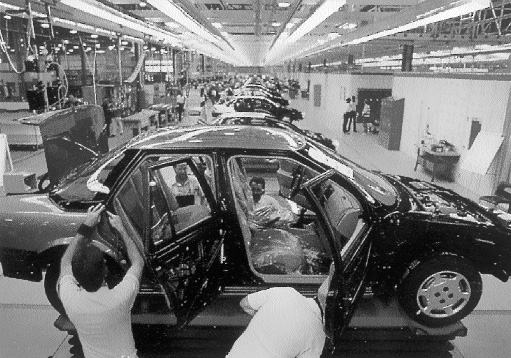
Завод HONDA в г. Мэрисвилле (США, штат Огайо) предоставляет идеальные возможности наблюдать под общей крышей все функции современного сборочного производства. Поставка и разгрузка производятся мелкими партиями, и приемочные площадки оборудованы таким образом, чтобы соблюдалась подача соответствующих изделий на сборку в определенной последовательности. На одной площадке, например, разгружаются сиденья, поставляемые фирмой GENERAL SEATING OF CANADA LTD., на другой — двигатели с завода HONDA в Японии и контейнеры с сырьем из Германии для вакуумного формования щитков приборов и бамперов.
Сборочный завод сам штампует 80 главных кузовных панелей и основных деталей кузова, и пока на разных участках завода осуществляются операции подсборки узлов будущего автомобиля, в кузовном цехе начинается соединение отштампованных панелей кузова. Сначала мелкие детали свариваются в подсборки и соединяются с панелями основания кузова, к которым затем привариваются кронштейны и усилители. Комплект основания движется по конвейеру, соединяется с панелями крыши, передней стенки и багажника, после чего все это сваривается с боковинами на позиции, называемой «главным сварщиком». Когда зажимы «сварщика» схватывают части кузова, сотня электродов извергает сноп искр и через несколько секунд возникает кузов, который на следующих позициях окончательно скрепляется тысячами точек сварки. На этих этапах большая часть сварки производится автоматически роботами.
Кузов с установленными дверями покидает кузовной цех, и поступает в цех окраски, где сначала проходит операцию погружения в ванну с грунтом, легкую пескоструйную обработку, а затем поступает к роботам-уплотнителям, которые наносят слой уплотнителя и покрывают днище слоем поливинилхлоридного звукопоглотителя. На следующем участке каждый кузов получает дополнительно около 2 литров грунта-уплотнителя, очищается продувкой сжатым воздухом, обеспыливается мягкими щетками и протирается вручную ветошью. Когда он тщательно очищен, на него наносится примерно 3,5 — 4 литра основной краски и еще 2 литра защитного бесцветного покрытия. После сушки в течение часа в печи качество покрытия проверяют вручную, и кузов поступает на окончательную сборку.
На первой позиции снимаются двери, чтобы на отдельной линии произвести их подсборку. Этим предотвращается их возможное повреждение и облегчается работа сборщиков по установке дверной арматуры, стеклоподъемников и т.п.
Сборка силового агрегата и кузова происходит на параллельных линиях. Когда кузов принимает законченный вид на последних операциях после укладки ковриков, монтажа консоли с рычагами переключения передач и стояночного тормоза, его поднимают, и собранный на параллельной линии силовой агрегат, включая подрамник, стойки подвески, рулевое управление и другие элементы, устанавливается на свое место происходит так называемое «обручение». На этой операции занято три человека, и длится она 60 с, пока производятся все присоединения и затягиваются болтовые соединения. Затем монтируются выпускные трубы, прокачивается тормозная система, на автомобиль устанавливаются колеса.
После схода автомобиля с конвейера производится установка заднего и ветрового стекол. Последние операции сборки — подсоединение систем в подкапотном пространстве, установка рулевого колеса и, наконец, дверей. Готовый автомобиль проходит ряд испытаний и регулировок, прежде чем будет отгружен с завода.
Описанный процесс типичен сегодня для массового производства и при хорошей организации обеспечивает требуемый уровень качества и производительности труда.
В заключение для сравнения приводим данные производительности разных автомобильных компаний.
При подготовке статьи использовались материалы журналов «Автомобильная промышленность США», «АМЕРИКА», проспекты компаний ГАЗ, TOYOTA и NISSAN.